Highrise Design has started lab-testing on various bolted joints to determine the optimal remedy against unfavorable corrosion of aluminium structures in offshore & marine applications. A first test piece has recently started a 1.500 hrs salt spray test to provide further insights in best available solutions.
A common perception is that Aluminium is a non-corrosive material. But actually, the contrary is true: aluminium is extremely corrosive. But its specific corrosion-process will form a thin protective layer of aluminium oxides, shielding the material from further oxygen access. With that protective layer in place, the corrosion process of aluminium normally comes to an early halt.
Galvanic corrosion
However, under certain circumstances this ideal situation gets hampered: a mechanism known as galvanic or bimetallic corrosion can cause sustained corrosion of aluminium. Galvanic corrosion may occur when two dissimilar metals are in contact with another while an electrolyte is covering the connecting area. The electro-potential difference between the two different metals is a driving force for an accelerated corrosion attack. If aluminium is the more anodic of the two metals in contact, this process is dissolving the aluminium into the electrolyte. In this way aluminium may corrode far more rapidly and to a much bigger extent than in normal atmospheric conditions. Especially in seaside, maritime or offshore applications, where sodium chloride (sea salt) containing water can cover the metal connections, an ‘ideal’ galvanic cell is created. This can possibly have considerable impact on structural integrity.
Bolted joints in Aluminium structures
Aluminium structures often contain bolted joints. These joints need to be carefully designed to avoid galvanic corrosion between the aluminium structure and the metal bolts. Selecting proper materials for these bolted connections is however not easy: various solutions all come with their pro’s and con’s. A simple way forward would be to avoid the use of different metals in a joint by using aluminium bolts. This would definitely resolve the problematic dissimilarity of metals in the connections. But aluminium bolts are not nearly as strong as steel bolts, making this solution quite unfavourable in terms of efficiency in space and costs.
Using (carbon) steel bolts is possible, but only when separating the aluminium and the steel bolts, using washers and bushes of inert materials. The disadvantage of these elements (next to costs and space-requirement) is that these need to endure challenging circumstances in lifetime. Most inert materials are prone to aging: deterioration resulting from UV-radiation and damage inflicted by icing conditions. In practise these materials often decay early, possibly resulting in loose bolt connections.
The most practical solution over last years has been the use of stainless steel bolts (A4 or A5 quality) directly connected on the bare aluminium. The shielding layers of oxides on both aluminium and stainless steel have a low potential difference. This results in a relatively mild form of galvanic corrosion of the aluminium material, mostly around the bolt heads. Although it can be visually disturbing, in most cases this corrosion remains minor, not impairing the integrity of the joint. However, in certain circumstances, even this ‘milder’ galvanic corrosion process can still cause unacceptable corrosion. Especially in more aggressive, acidulous environments the galvanic corrosion needs to be better prevented to ensure proper lifetime expectancy of the aluminium structure.
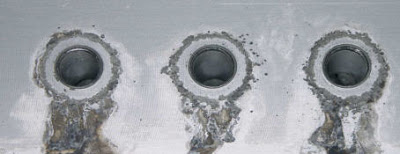
Metal-coated bolts
A big step up can be achieved by the use of specially coated bolts. A broad range of thermally metal-coated bolts is available in today’s market for fasteners. Nowadays, many of these coatings do OK on the subject of possible Hydrogen embrittlement of the bolts. These coatings are primarily aimed in protecting the steel bolt itself from ‘regular’ atmospheric corrosion. But it these coatings also open another mechanism: by selecting a metallic coating that has a very limited dissimilarity towards aluminium, also the galvanic corrosion of the aluminium structure can be positively influenced. The use of Dacromet/Geomet coated bolts have shown remarkable improvements, for instance on truck-chassis that endure corrosion from the salty conditions of wintery roads. A study in Japan (2016) by Nagoya University on joints in bridges was similarly positive on the effect of metal coated bolts.
Similar improvements may be expected in maritime and offshore conditions. But the available manufacturers data on these metallic coatings is until now still only focussed on the protection of the bolt itself. Not much information is available on the aspect of galvanic interaction with aluminium.
Salt spray test
To generate further insights in the effecivity of various coatings, Highrise Design has initiated a series of salt spray tests, to compare the influence of various available metallic coatings on galvanic corrosion of bolted aluminium joints.
Two weeks ago, a first test piece of bolted plates of aluminium has been placed in the salt-spray cabinet at M2 lab in Udenhout to endure 1500 hours of spray-testing according to ISO 9227-NSS.
This first test piece is expected to provide comparative results for 4 different aluminium to aluminium connections:
- Untreated stainless-steel bolting (A4 quality)
- Zn Al flake coating (Geomet 500A)
- Zn Al flake coating (Delta Protect KL 100)
- Duplex Coating (Stafa P2000)
So now we are obviously impatiently waiting for another 7 weeks for these first results…